We disassembled our 70-year-old Slot Machine!
Remember that 70-year-old slot machine that we acquired back in February through our Croatian Connection? Of course, you do! If not, jump over to the original article, you can find it here: some cool photos and an introduction to the slot machine.
In that article we revealed that our old-timer has been fighting an unfair battle against time for almost 70 years, to help him out, we’re going to restore it to its former glory and beat the clock!
Now, in this article we’re going to go through the disassembly process in which we will show you how we pulled apart the machine down to the last piece. Of course this wouldn’t be a good intro if we didn’t start with a clickbait heading, right?
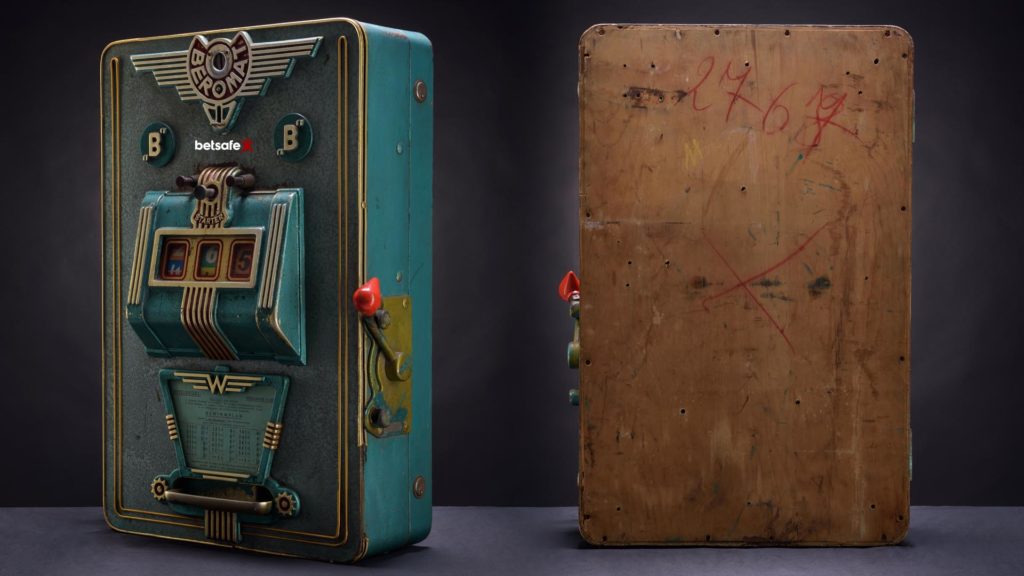
What we found inside will surprise you!
Nuts, slotted screws, wingnuts, a bit of metal, some wood, and drops of glue here and there, as well as a…. Wasp’s nest. Yep, someone wasn’t paying rent for quite some time it seems, and we had to be the ones to bring an end to it:
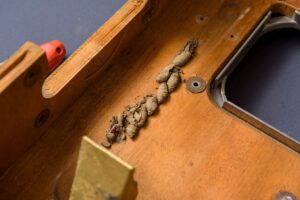
The dormant tenants left a muddy mess, cocoon-like empty shells. So it seems they were the bunch who took the opportunity to have an “it’s free real-estate” moment, probably during the time when the slot machine ended up jobless in a dark corner of some Austrian shed. We did not even manage to put an eviction notice; the guys were already on their way before we got a chance to talk to them. Thankfully, the litter they left was easily reprimanded, and no major damage was done to our precious wooden housing.
But, that tenant aside, it’s rather unbelievable how easy it was to open the back of the machine. It sits on two hinges and it’s closed shut by two locks placed on the door’s side frame, one close to the top edge, and the other one to the bottom edge. That is so the door can evenly close up once you turn the key.
Speaking of, unfortunately you won’t get that feeling of preparing up for a rocket launch with turning two keys simultaneously, because we only got one key, and both locks work with it. But hey, you can still pretend that you are opening up an old treasure chest because it sure does remind us of one.
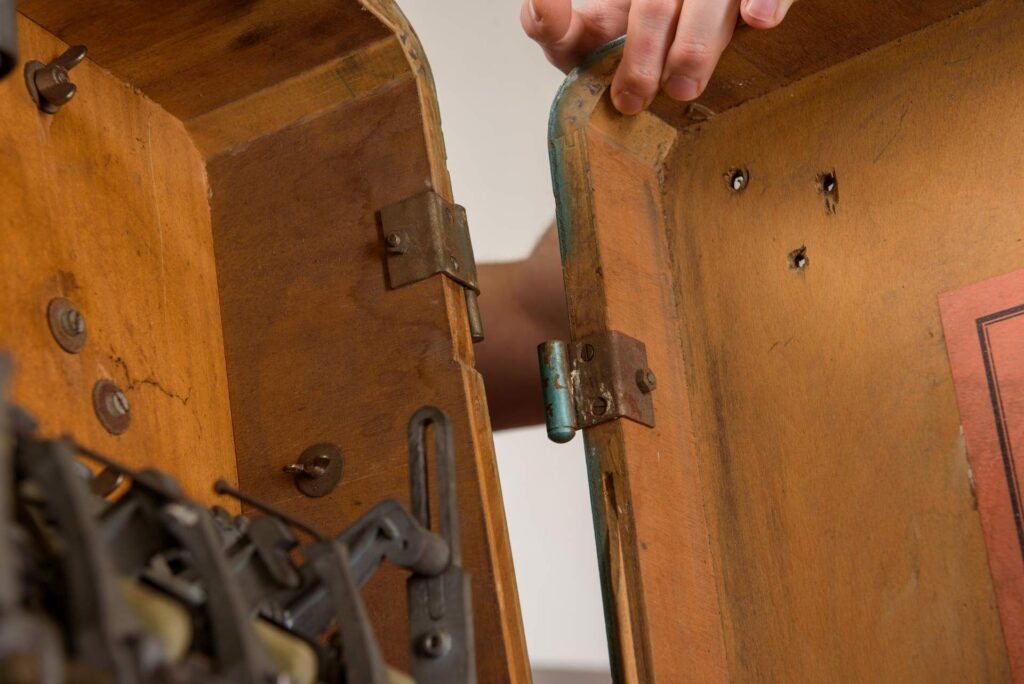
Once the door was out of the way (it just slides off the hinges), with the help of an 8- and 10-mm wrench, and a 1 mm thick flat-headed screwdriver we managed to disassemble almost the whole machine. We were surprised how it all went down so fast once we started going at it, almost like handling a 70-year-old Lego set – but without stepping onto any of the pieces on the floor.
I mean sure, we are talking about the early 1950s, they kept it simple because they could. It’s not like they had a choice of CNC machines and 3D printers to make super complicated one-off mechanical parts.
Although it does need two people to move it around, it seems that Mr. Keutschacher, who oversaw the servicing and repairs of our Beromat slot machine, didn’t go through too much hassle of keeping it running all alone. Despite looking scarily complicated when you first open it up, once you get going and start taking things off, everything makes perfect sense and is easily handled by a single person.
Meet the three Mouske… Column reel wheels
To disassemble the insides of the machine first we had to take out the star of the show, the main mechanical assembly that holds the three-column reel wheels. Luckily, four nuts later it just popped right out and we placed it on the table where our eyes got to take a better look at it. This is probably the second heaviest thing besides the slot machine as a whole, it weighs at least 12-15 pounds.
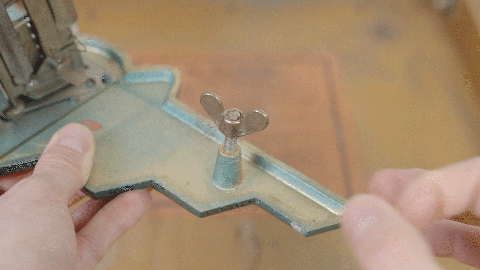
This doesn’t come as a surprise as everything is made out of metal alloy, in particular, the MAZAK (now known as the ZAMAK), which has zinc as a base metal, and alloying elements such as aluminium, copper, and magnesium. It seems that this type of metal alloy was used throughout the whole mechanical assembly, while the outside metal parts had an additional gold-like layer of coating, probably for additional surface protection, plus the final aquamarine waterway texture on top of it.
These transitions of the different surfaces and paints can be seen on the coin tray as it’s pretty scuffed up from coins slinging around in it, so it looks like that we still have the original fit and finish in our hands. This old way of doing things back in the day gave our slot machine that little bit of extra something. It really feels like you’re holding a piece of history, not just because you know that it is a piece of history, but because it gives that away with every single interaction you have with it.
After taking a detailed inspection of the main assembly, we realized that each reel is a separate piece on its own and they are all aligned on a single shaft that can easily be removed from it. Thankfully, all the springs were “baked” in place and lost their bouncy-bouncy property, so we didn’t have any fear of them flying past our heads while we were disassembling the reels.
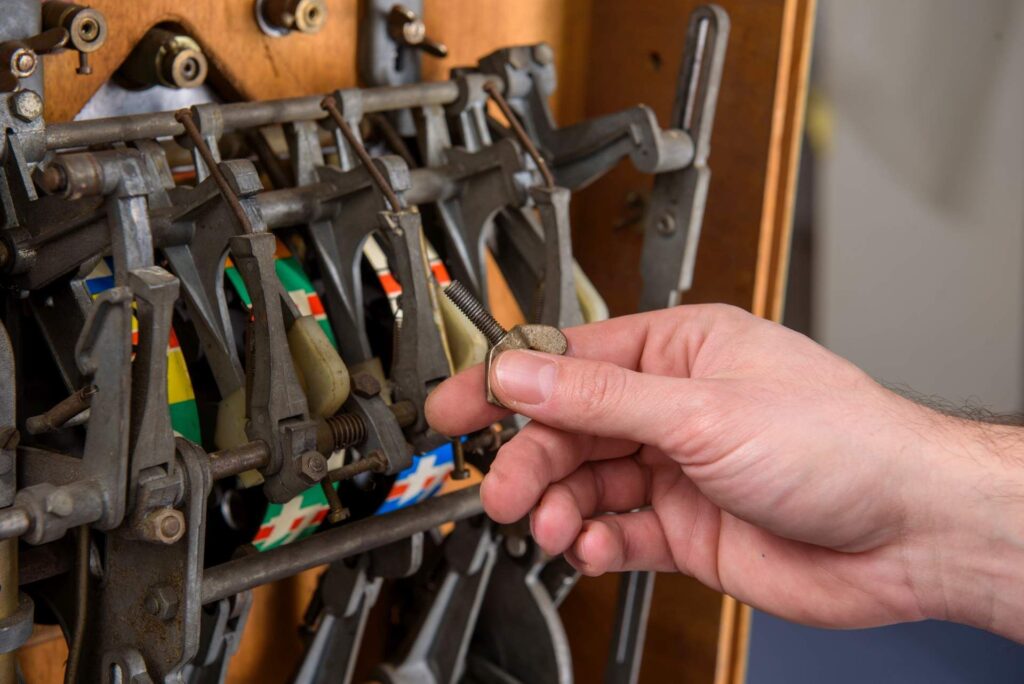
On the left side of it you can see two bronze-coloured coin-gathering tubes that guide the coins through a winning and “house” pool. Opposite of it, you have the secret ingredient, a magneto-mechanical contraption that controls the reels speed and stopping point once the player pulls the handle.
Once this main assembly was out of the way, the slot machine shaved a lot of pounds, making handling it easier, so we could play with the rest of the elements in it, such as the coin funnelling system.
It sits right above those coin-gathering tubes and acts as a system that guides them in their path, probably going – one for you, three for us. A big coin guide rail leads them to it from the coin insert point on the front, which looks like some kind of medal of honor for an airforce officer.
As you can see from the photos that the coin rails are partially hollowed out, as if someone used a hole-punching tool on it, which was probably the point-of-entry for our buzzing friends as they smuggled their way in.
Proceeding to pull off some non-functional pieces, everything is held from the inside out, so you as a player don’t have to look at all those screws and nuts. The reel “screen” cover is the biggest part outside the slot machine’s inner compartment, it’s also pretty heavy as it holds thick sheets of glass separating you from the reels. What also holds some glass is the owner’s nametag, but interestingly enough, one of the two “windows” had an acrylic type of see-through cover instead of glass. So, it seems that it was broken at some point and replaced with a modern, less fragile solution.
It was interesting to see how the printed paper with the names held up, does not seem to have any drinks spilled onto it, looks well preserved. The thing that does unveil its age is the writing style, which definitely wasn’t something from Windows’s XP font list. Maybe OPTI Edwallian? :shrugs:
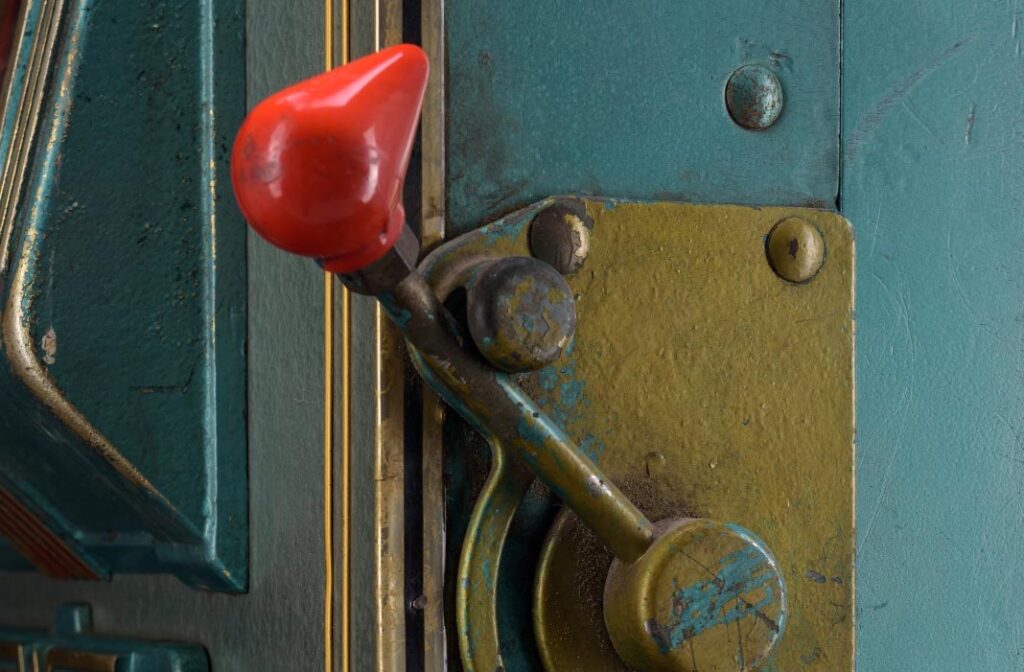
A woodchuck and a duck enter a bar…
Besides getting off the other fixed pieces, like the coin tray and dispenser, the only functional mechanical parts left are the lever handle and the play trigger system. Those are the pieces that get things going when going gets tough, after all it requires players input to turn it over and get it started.
This is done by using the main side handle lever on the right, which… Do you know how people were on average shorter back in the day than now? It seems like they also had smaller hands because the red top handle part you grab onto to pull it down is really smallish.
Anyhow, in order to mount this assembly, engineers had to make a special cut-out portion on the side of the front frame, while from the inside it connects to a complex system of levers, rods, springs, and a big main cylinder. We don’t even have to tell you that everything makes that loud, satisfactory click and clack sounds when you pull it down. The next best thing to a mechanical keyboard if you ask us.
Finally, with every single piece out and off the housing, we were left with two empty wood veneer shells (plywood by the looks of it), those being the front panel and the back door. The weight difference, or what’s left of it, is impressive. It’s hard to believe that it can hold that much weight in it. This type of wood can be great in the long term even if left alone in atrocious conditions, and it seems like ours somewhat withstood the test of time, with a few nibbles on some spots. Maybe a woodchuck did that to find out how much wood could a woodchuck chuck if a woodchuck could chuck wood?
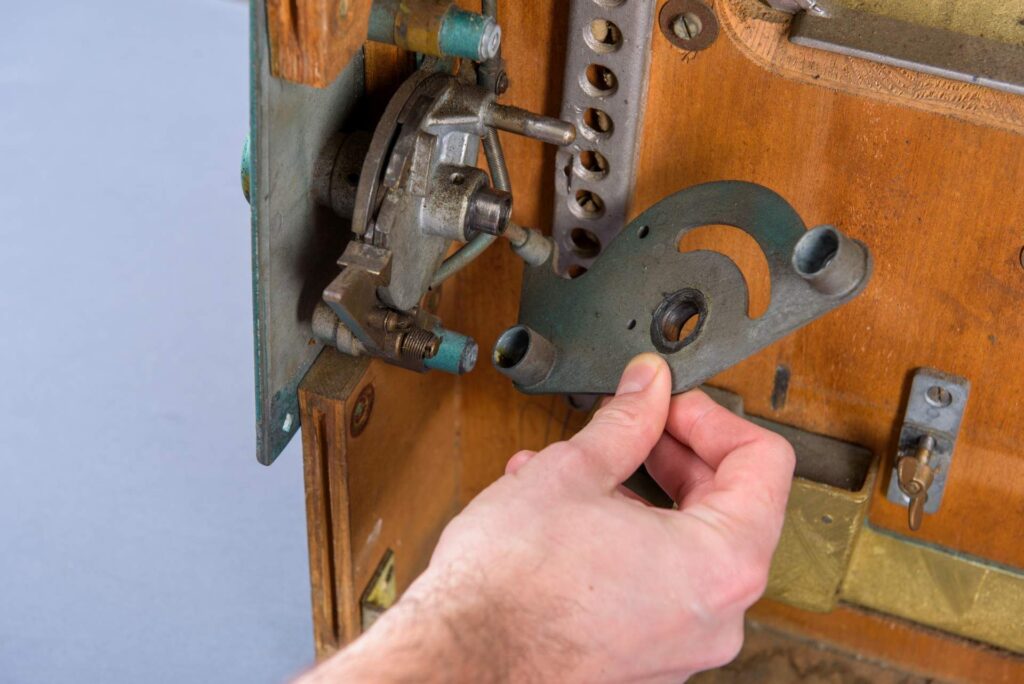
Luckily for us, apparently not a lot. Either way, we’re not too worried about it, because there’s still plenty of the same material used in today’s workshops, which puts us at ease in case something needs to be re-done.
With the Beromat slot machine completely turned upside down, and inside out (professional term would be – “Dora the Explorer” the shiznit out of it), we get to the part where our hands get dirty, eyes full of sanding dust, and nostrils full of paint fumes.
This next step is what the restoration is all about, getting our slot machine to its full former glory, we even dare to say that it will turn out even better than the original! The plan is to first strip down the old paint, to see what is hiding behind it – are we good to go with original housing and splash it with some new colour, or is some woodwork required? After that, we’ll be checking out all the mechanical bits in detail, which is a big task for itself, before all we have to test them out to see if they can still do their thing and get the good ol’ reels up and running. By the looks of what we saw during our disassembly, some cleaning and oiling up will be mandatory, possibly even some parts replacement.
Either way, as it is we are already having a reel blast with it, our Austrian schillings are already on their way from eBay! We’ll have enough time to polish them out before we can slot a couple of them into our freshened-up Beromat, hopefully already at the beginning of May. Before we forget, if you would like to check out the “behind the scenes” article, you can do so under this link.
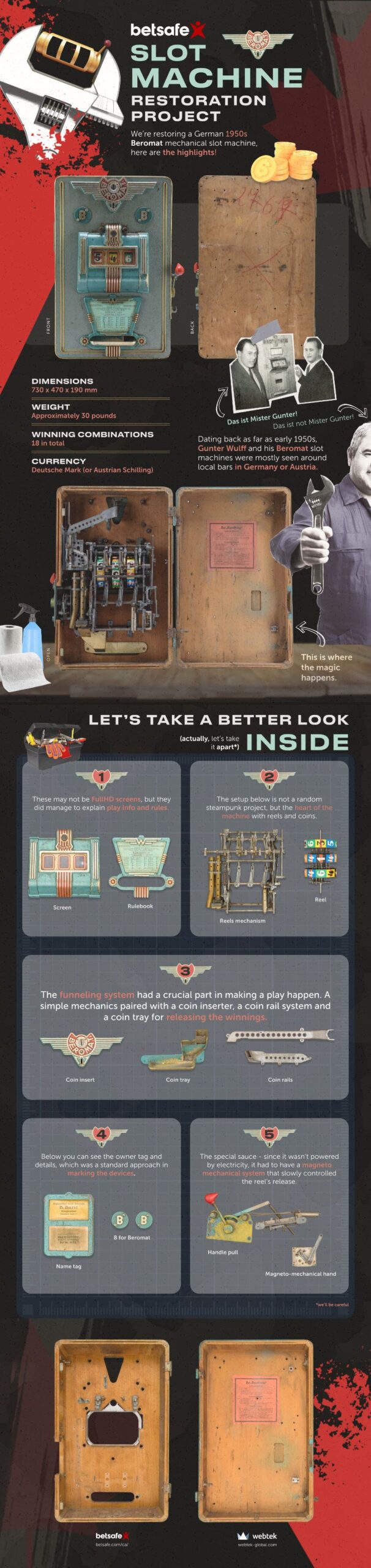